Home / R&R Academy / Case Studies
Case Studies
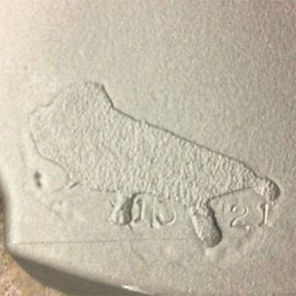
Participate in a Case Study
Has R&R helped you make a minor product or process change or a complete system overhaul? Want to share your thoughts with your fellow casters?
Email our marketing team at: Marketing@ransom-randolph.com.
Ceramic Shell

Additives Impact Shell Properties (Matrixcote® system)
The addition of fibers and polymers used in the Matrixcote system slurries positively impacted shell properties
-
Fibers
-
Increased shell thickness
-
-
Polymers
-
Increased green strength and green deflection (elasticity) of the shell to reduce shell cracking during dewax
-
Decreased post fired shell strength to aid in shell removal
-
-
Fibers and polymers
-
Offered potential for coat reduction due to increased shell strength and thickness per coat
-
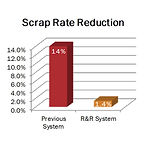
Complete System Conversion
Within a month of converting the primary slurry to Primcote binder, Foundry F
requested a proposal for a complete system overhaul
-
Reduced coats from 9 to 7
-
Reduced scrap rate from 14% to 1.4%
-
Annual material savings: $19,200

-
Created more uniform edges
-
Eliminated 2 backup coats from existing process
-
Labor savings: $50,000 (approx.)
-
Eliminated 1,000 hours of labor time
-
-
Reduced scrapped parts
-
Savings: $37,000 (approx.)
-
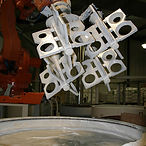
Foundry 1
-
Significantly improved slurry life to 22 months (more than 3 times previous slurry)
-
20% cost reduction versus previous slurry
-
Reduced costs associated with dumping and rebuilding slurry
Foundry 2
-
Significantly improved slurry life to 9 months (nearly 5 times previous slurry)
-
32% cost reduction versus previous slurry

-
Reduced post fired strength by 35%
-
Increased permeability by 128%
-
Reduced cracking on round ring parts
-
Significantly decreased scrap and rework with positive metal on parts
-
Eliminated gas defects on certain parts
-
Reduced make up time from 60+ minutes to 20 minutes
-
Simplified slurry maintenance
Solid Mold

-
Reduced mold cracking
-
33% increase in green (wet) compressive strength
-
Reduced finishing coats and improved as-cast surface finish
-
Surface tension agents reduce air bubble defects
-
Tighter tolerances, plus reduced warping and cracking
-
Superior thermal stability